Client
Industrial and Railway Transformer Manufacturer
Application
Transformer and Choke Type Testing
Date
2021
Introduction
Heat-run tests are essential in verifying the thermal performance of transformer, choke and motor designs, ensuring they meet operational requirements under rated conditions. A critical aspect of these tests is determining the maximum internal winding temperatures, as excessive heat can compromise efficiency, insulation integrity, and overall lifespan.
To accurately determine the maximum internal winding temperature, cyclic measurements of winding resistance are performed during the cool-down phase following the heat-run test. This approach provides precise insights into the thermal behavior of the windings under load. Importantly, this procedure must be conducted for all windings of the DUT to ensure comprehensive evaluation and compliance with design standards.
Challenges
Heat-run measurements face several challenges that require careful management to ensure accuracy:
- Temperature Variability: Winding temperatures decrease unevenly during cool-down, requiring precise timing and instruments.
- Resistance Accuracy: Small errors in resistance measurement can lead to significant temperature estimation inaccuracies.
- Access to Windings: Measuring all windings in complex transformer designs can be challenging.
- Time Sensitivity: Measurements must be done quickly during the limited cool-down period.
- Environmental Impact: Ambient conditions like temperature and humidity can influence results.
- Safety Risks: High temperatures and electrical hazards require strict safety protocols.
- Data Complexity: Accurate analysis of resistance data requires expertise and precision.
OUR SOLUTION
Heat Run Resistance
Measurement System GRM1000
The GRM1000 Heat Run Resistance Measurement System provides a state-of-the-art solution for accurately measuring winding resistance after heat run testing of transformers, motors and other industrial equipment. The DUT is connected to the measurement system prior to the heat run test. The voltage proof inputs allow a permanent connection during the heat run test. After the heat run is completed, the system is activated to perform cyclic resistance measurements with precise timing on all configured windings. Our software controls the entire measurement system and transfers the data to the PC. The internal overtemperatures of the device under test are determined from the measured data. The system has flexible reporting options and allows easy export of data to standard formats such as CSV and Excel. Designed for accuracy and efficiency, the system provides reliable data acquisition. Our solution simplifies complex testing processes, making it ideal for both product validation and routine testing. Discover how the GRM1000 can enhance your testing efficiency and accuracy.
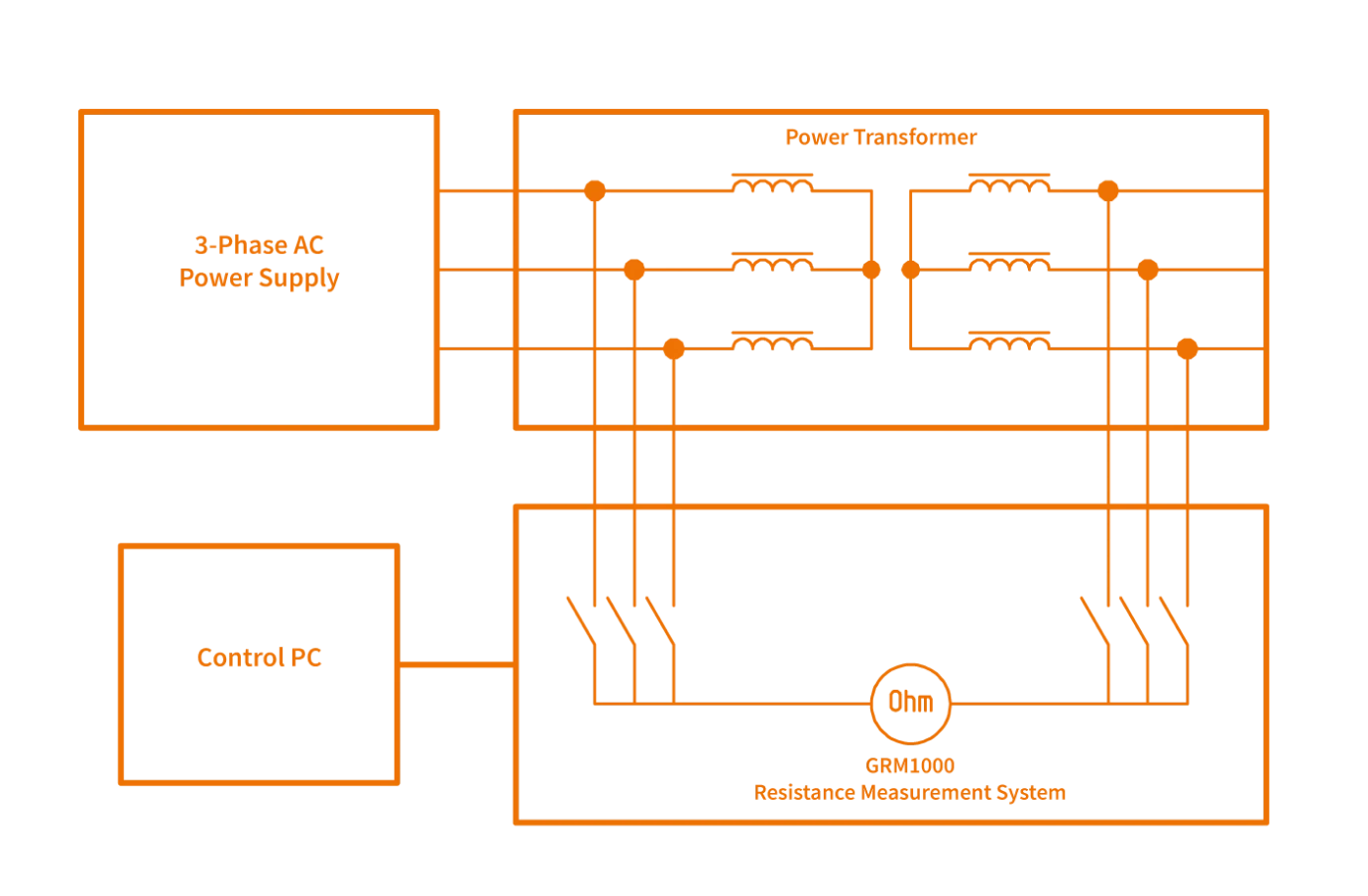
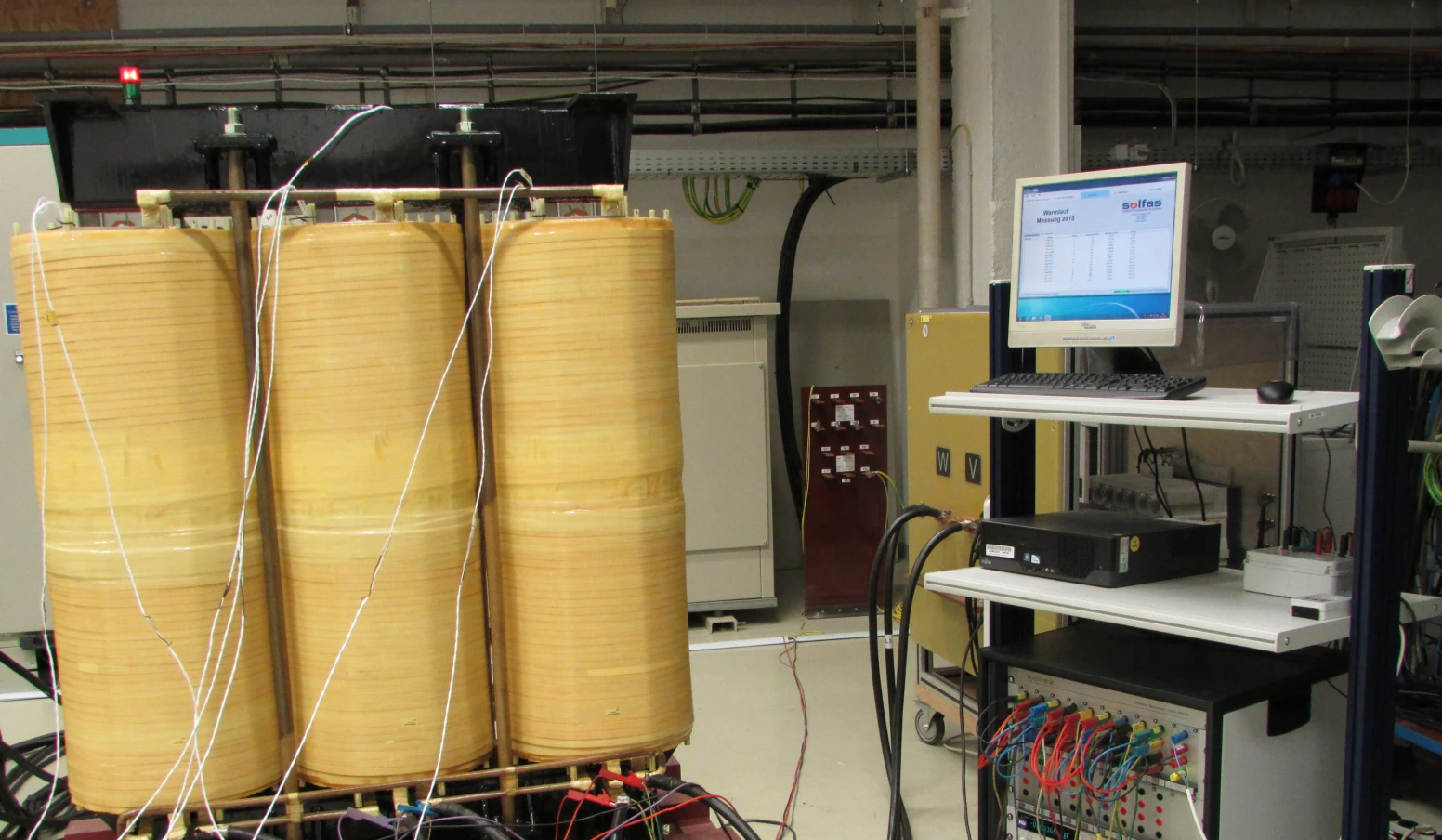
Highlights
Heat Run Resistance Measurement System
Features
Heat Run Resistance Measurement System
Flexible Testing Sequence
The number of channels and the timing can be adjusted. Each channel can be configured with individual name and test current.
Evaluation and Report
The Excel based calculation of the internal DUT over-temperatures allows easy modifcation and customized reports.
Networking with Ethernet and WIFI
For easy integration into vaious test setups and mobile use of the system.
Remote Control
The system and all instruments are fully remote controlled for convenient operation from the desk or control room.
PC Control
Full system operation can be managed directly from PC.
Export to CSV and Excel
The data can be easily exported to CSV and Excel. This enables simple customized evaluation and documentation.
Measurement Values
Heat Run Resistance Measurement System
Winding Resistances
Measures the resistance of all DUT windings after heat run test.
Winding Temperatures
Calculates the internal winding temperatures based on the resistance data after heat run.
Ambient Temperature
Monitors the environmental temperature during testing.